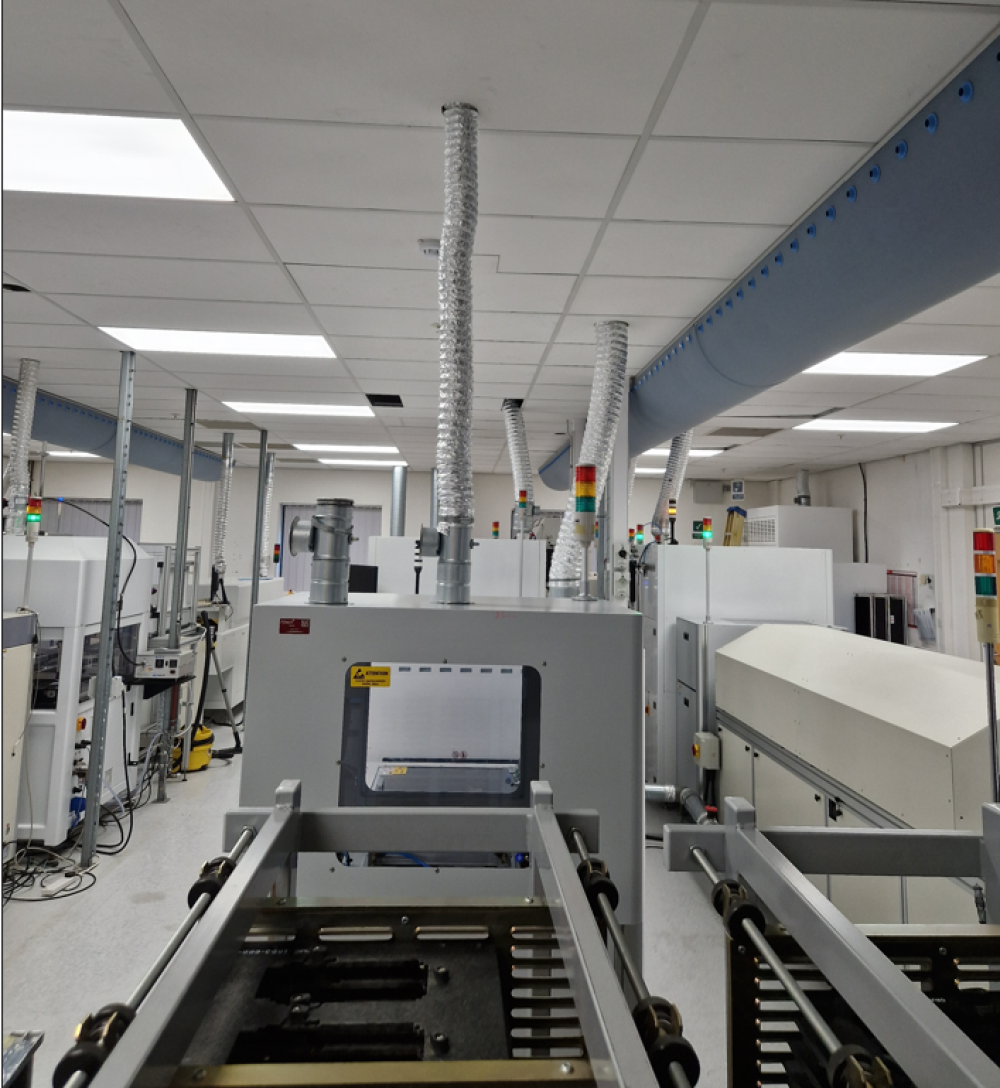
Installation For A Conformal Coating Extraction Line
The objective was to install a 9000-5000i volume control filter and ductwork system for a conformal coating line.
The system layout is as follows: The ductwork configuration features a 200mm diameter ductwork connected to the filter, extending vertically through and above the suspended ceiling. A single line of ducting runs above the ceiling, gradually reducing from 200mm to 80mm in diameter, serving four extraction spigots. Near the start of the duct run, a 150mm diameter branch extends at a 90-degree angle to a fume extraction cabinet. Each extraction point is equipped with foil-type flexible ducts descending through neatly cut ceiling holes, connecting to volume control dampers for balancing.
Project Challenges
- Machine Installation Delay: During our recent project, we ensured all preparations were in place for the final machine in the production line. Although the machine was not available during the project timeline, we proactively capped the last connection and left the flexible conduit in the ceiling, ready for the customer’s easy connection upon its arrival. This approach guarantees a smooth and efficient commissioning process once the machine is on-site.
- Access Issues: Working with an existing line of machines presented access challenges, particularly in areas above the suspended ceiling. However, our team expertly navigated these constraints to ensure seamless operations.
- Existing Services: Navigating around existing services such as heating and ventilation ductwork, sprinkler pipes, and electrical service trays above the ceiling tiles posed a significant challenge. Despite this, we successfully established an efficient duct route, showcasing our problem-solving skills and dedication to delivering top-notch solutions.
Health and Safety Measures
- Ensured the health and safety of all employees.
- Complied with all relevant regulations.
- Maintained ambitious standards of quality throughout the project.
Solution
To address these challenges, we strategically removed ceiling tiles at key points, allowing us to feed the ducting into the ceiling void. The ducting was then suspended from threaded bars and gripple wire brackets. Using a variety of power and hand tools, and with access provided by two ladders, we successfully installed the extraction system.
Key Features of the Solution
- Strategically Installed Ducting: Ensured optimal placement despite access challenges.
- Compliance and Safety: Adhered to all health and safety regulations.
- Versatile Installation: Utilised a variety of tools to complete the installation efficiently.
- This highlights our ability to adapt to unforeseen challenges and maintain exacting standards of safety and quality throughout the project.
Implementation
- Site Assessment: Over the course of a few days, our LEV (Local Exhaust Ventilation) Engineers arrived on site, attended a brief site induction, and were greeted to the site liaison.
- Project Area Inspection: We inspected the project area and without any issues, began unloading all equipment and materials into the designated work area.
- System Design: The system design included a transfer station, and a vented cupboard equipped with a Delta Therm 300 CFM unit.
Training and Support
Purex provided comprehensive training for the employees on how to operate and maintain the new system. Ongoing support was also offered to ensure the system’s optimal performance
Conclusion
We successfully installed the 5000i system specifically designed for conformal coating extraction. This installation ensures efficient extraction and precise volume control for the conformal coating line, meeting all project requirements and standards.
This detailed case study highlights our expertise in handling complex installations and our commitment to delivering high-quality solutions that meet our clients’ needs.

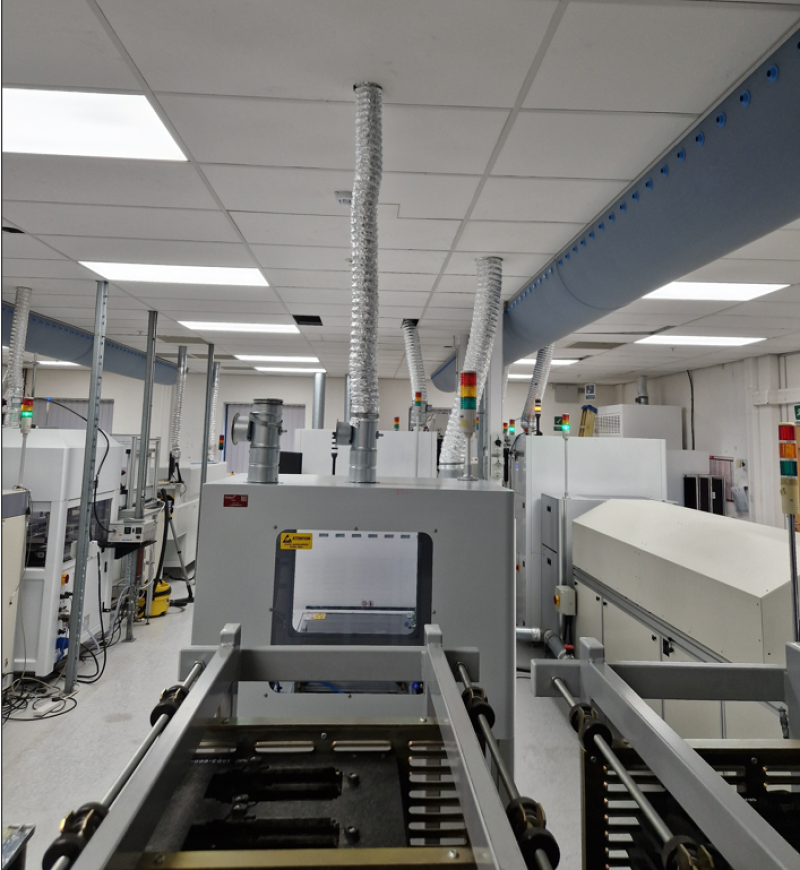
Used Product
-
5000i
5000i
The 5000i 3 Phase offers a choice of pre-filters depending on if your workspace allows side inlet or rear inlet. This machine is able to extract from up to 36 separate Purex arm kits simultaneously, making it an ideal choice for large scale Hand Soldering processes. Its large air flow also allows it be used for Wave Soldering applications where a steady and constant airflow is needed. In addition, it can be used on large scale Laser Engraving and Coding processes.
View product
LEV Engineers Input
‘Our overall experience at this site was a pleasant one. The personnel on the site were extremely helpful and the welfare facilities were second to none.’
Need help choosing?
Speak to a member of our expert team to help choose the most suitable machine for your requirements.